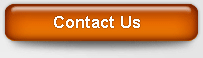
Process Safety
services include the investigation of explosions in the Chemical Process Industries and the implementation of design changes, process safety studies and HAZOP reviews.
Flashback Prevention
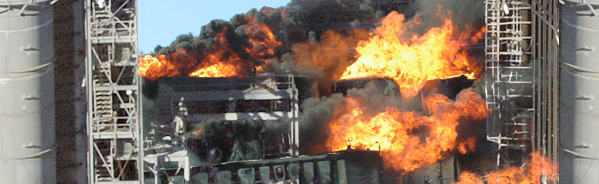
Heat Transfer
Flashback prevention helps cure thermal oxidizer explosions
System redesign improves safety and productivity
Chemical Processing, January 1997 - Rocky C. Costello, P.E.
A vertical thermal oxidizer was used in a Gulf Coast chemical plant to incinerate vapors from tank-truck cleaning, tank farm and batch distillation operations.
Over a period of 2 years, a number of explosions had occurred at the thermal oxidizer. The last explosion was the most severe, resulting in the destruction of the spark-proof booster blower that drew air from the tank-truck filling and cleaning operations.
The normal procedure was to blanket the incoming truck with inert gas. A special manway cover with connections for inert gas, inert gas exhaust, exhaust air for drying, and cleaning solvent was fitted to the tank truck.
This purged out all the air containing flammable hydrocarbons. Once this inert purge cycle was completed, cleaning solvent was circulated via the manway to a cleaning head. The solvent flowed from the discharge of the truck to a tank and was then pumped back to the cleaning head.
The final cycle consisted of an air drying purge. The explosions had all occurred during the air drying purge of the truck.
In order to solve this problem, the chemical plant made several flashback-prevention modifications. These included the installation of flame arresters, averaging pitot tubes, thermal detectors, a dilution air control valve, draft electronic DP cells, a low-pressure selector, a square-root extractor and a three-way solenoid valve.
Flashback mechanism
As the drying air pushes out the flammable gas mixture, it moves down the pipe to the booster blower and on through more piping. If the linear velocity in the pipe is too low, a flashback that results in an explosion can occur.
Flashbacks occur when the stream velocity near the wall falls below the burning velocity.
The thermal oxidizer was a vertical unit with a gas-fired burner in the center. A donut ring with six nozzles that injected vapors from plant operations surrounded the burner.
There was one inlet nozzle to the donut ring from the discharge of the booster blower. This was later modified to four equally spaced inlets to the donut ring to provide better distribution to the six nozzles inside the thermal oxidizer.
After the last and most serious explosion, a redesign of the system was undertaken with a primary goal of maintaining high average gas velocity in the pipeline. The redesign improved the safety of the system through the addition of a number of important features. They include:
-
Adding flame arresters, with temperature measured at the flame arrester discharge.
-
Installing the automatic addition of dilution air to increase average gas velocity when necessary.
-
Dilution air is activated by a measured drop in the average gas velocity.
-
Equalizing the distribution of gas flow into the six entrance nozzles on the thermal oxidizer.
-
Reducing the diameters of the inlet nozzles ahead of the unit to provide further increases in velocity.
-
Balancing pressure drops for each piping section from the fan and going into the donut ring.
Flashbacks into pipelines with air-hydrocarbon mixtures occur when the flame speed is greater than the process gas speed. For most organics, a discharge design speed of 4.5 m per sec (average across nozzle diameter) is adequate in pipes Ids up to 300 mm (~12 in).
Some compounds that require higher speeds are ethylene oxide, acetylene and hydrogen. In the case described, 6 m per sec was used as an added safety factor. Redundancy was built into the system at many levels.
Averaging pitot tubes were installed on each of the two piping legs on the discharge of the fan, and electronic differential pressure transmitters were installed on the averaging pitot tubes. The 4-20-mA signals from the differential pressure transmitters were converted to 3-15-psi pneumatic signals.
If the velocity drops below the design flowrate, the dilution air damper is throttles open until the velocity returns to a 6 m per sec. This is accomplished by bleeding in outside air.
A low-selector pneumatic instrument pressure switch ensures that the transmitter detecting the lowest flow is always chosen for control. The switch senses which differential pressure transmitter on each of the two averaging pitot tubes is lowered and allows that pneumatic signal to pass to the square-root extractor and on to the controller. In this manner, the leg with the lower flow becomes the control parameter.
Because flow measured by a pitot tube is not a linear function, a square-root extractor converts the signal from either of the differential pressure transmitters to a linear signal. The low selector switch determines which signal passes through. The damper actuator was fail-open.
Flame arresters equipped with thermal detectors were installed on each of the two piping legs on the discharge of the booster blower.
A pressure switch on the pneumatic line between the square-root extractor and the flow controller was set to activate the solenoid valve venting the air signal from the flow-recorder controller. This forced the dilution air valve into a fail-open position, which increases the linear velocity in the entrance nozzles any time a low-flow condition exists.
If the linear velocity in the pipe is too low, a flashback that results in an explosion can occur. Flashbacks occur when the stream velocity near the wall falls below the burning velocity.
All four of the pipe runs on the fan discharge are equivalent in length to ensure equal flow. The six 6-in nozzles entering the thermal oxidizer had Schedule 40 5-in x 6-in pipe reducers welded onto them in order to provide an even higher entrance velocity into the unit. Five-inch piping, while not commonly used in the chemical industry, is widely used in firewater sprinkling systems.
Castable refractory was placed around the six nozzles until it was level with the tops of the nozzles. This ensured that the nozzles did not get hot and oxidize. This increased the design velocity from 6 m per sec to 6 x (6.065-in ID/5.047-in ID) or 7.2 m per sec for increased protection.
There have been no flashbacks or explosions since the modifications were completed.
Please call for further information
R.C. Costello & Assoc., Inc.
1611 S. Pacific Coast Highway, Suite 302
Redondo Beach, CA 90277
Tel: (310) 792-5870, Fax: (310) 792-5877
E-MAIL: rcca[at]rccostello.com
COSTELLO
Consulting Engineers
- Explosion Investigations
- Hazards Analysis
- Published Article 1 (Flashback Prevention)
- Published Article 2 (Thin Film)
- Definitions