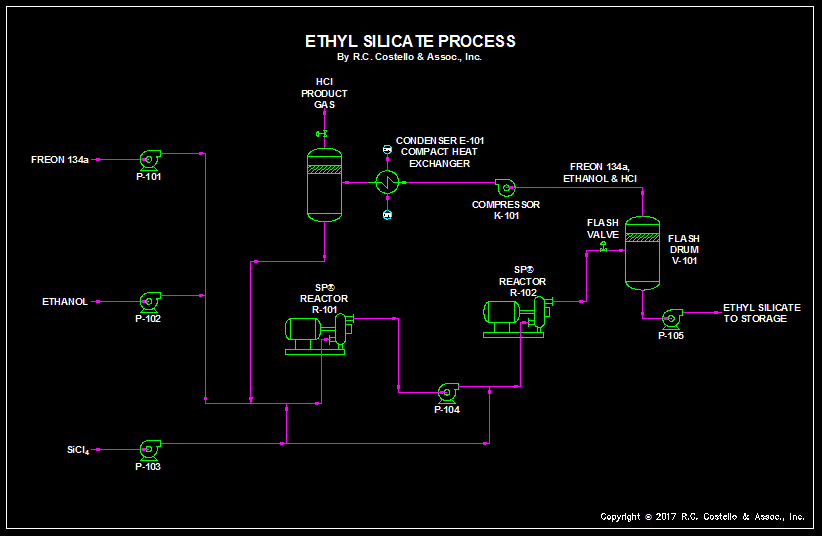
In the second part in this 2 part series of Building Reaction Flowsheets Utilizing Process Intensification, we show the production of ethyl silicate utilizing the Shock Wave Power Reactor by Hydrodynamics. This reaction system was originally a packed bed reactor followed by a large CSTR. In addition each reactor had a large distillation column associated with it to separate ethanol from hexane. The original chaser was hexane which was closer in boiling point to the excess ethanol and therefore much harder to separate. The flowsheet had an extensive number of pieces of process equipment.
Main Reaction and Side Reaction
In this example, silicon tetrachloride is reacted with ethanol to produce ethyl silicate (4-ethoxy silicon). The reaction chemistry is shown below:
SiCl4 + 4 C2H5OH ——————–> Si(C2H5O)4 + 4 HCl
The ethanol must be anhydrous because any water in the ethanol would react with the silicon tetrachloride as follows:
SiCl4 + 2 H2O ——————–> SiO2 + 4 HCl
Description of the Process with Process Intensification
A solvent, Freon 134a, acts as a chaser to help strip out the byproduct HCl. In the first reactor, the solvent, silicon tetrachloride and a portion of the ethanol are mixed and partially together. In the second reactor, the reaction of silicon tetrachloride and ethanol goes to completion further producing ethyl silicate and byproduct HCl gas. The solvent is a low boiling refrigerant that carries out the HCl. This goes into the overhead system where the excess ethanol and Freon 134a are compressed and condensed. They are finally recycled back to the reactor. HCl gas leaves the top of the separator drum.
A review of the boiling points shows:
Compound | Boiling Points | |
Hydrogen Chloride | -121.1°F | -85.05°C |
Freon 134a | -15.34°F | -26.3°C |
Silicon Tetrachloride | 135.8°F | -57.65°C |
Ethanol | 173.1°F | 78.37°C |
Ethyl Silicate | 336.2°F | 169°C |
In some portions of the plant the Freon 134a is a gas and in other parts it is a liquid.
A detailed computer simulation has not been prepared for this process, but at that time the liquid and vapor phases for the Freon 134a would be determined. In general, the ethanol is the excess reactant and silicon tetrachloride should be the limiting reactant which will be fully converted to ethyl silicate.
In summary:
- We have replaced the large reactors with small intensified units.
- The distillation columns were replaced with a flash drum by changing the chaser so the difference in the boiling points between the chaser and the ethanol are much higher.
- A compact heat exchanger is used as the two phase flow – cooler/partial condenser.
- Overall, the number of pieces of process equipment was reduced by over half providing a real savings in capital costs.
Let COSTELLO‘s team of highly experienced engineers help you with the process intensification of your chemistry and the modularization of your plant today!
Phone: 310-792-5870 Email: rcca@rccostello.com
Website: rccostello.com